Die letzten Wochen haben wir die guten Tage genutzt und den Stangenstahl auf der Decke verteilt. Dabei mussten wir nicht wie befürchtet große Teile der Schalung wieder abnehmen, den meisten Stahl konnten wir so platzieren. Nur die Schalung an der Nord-Ost-Ecke mussten wir entfernen um die dickeren Stangen unter die Gitterträger zu schieben.
Dieses Wochenende haben wir uns am großen Finale versucht. Im Vorgarten lagen noch 4 Betonstahlmatten vom Typ Q335A, 2.30 x 6.00 m, ca. 75 kg schwer. Um uns nicht einen Bruch zu heben haben wir die Matten schonmal auf 4.80 m gekürzt, bleiben noch ca. 60 kg pro Matte, die wir auf die Erdgeschoßdecke hiefen müssen. Letztlich haben wir die Matten senkrecht gegen die alte, 5 m lange Aluminiumleiter gestellt und zusammen mit der Leiter auf die Decke gehebelt und gezogen.
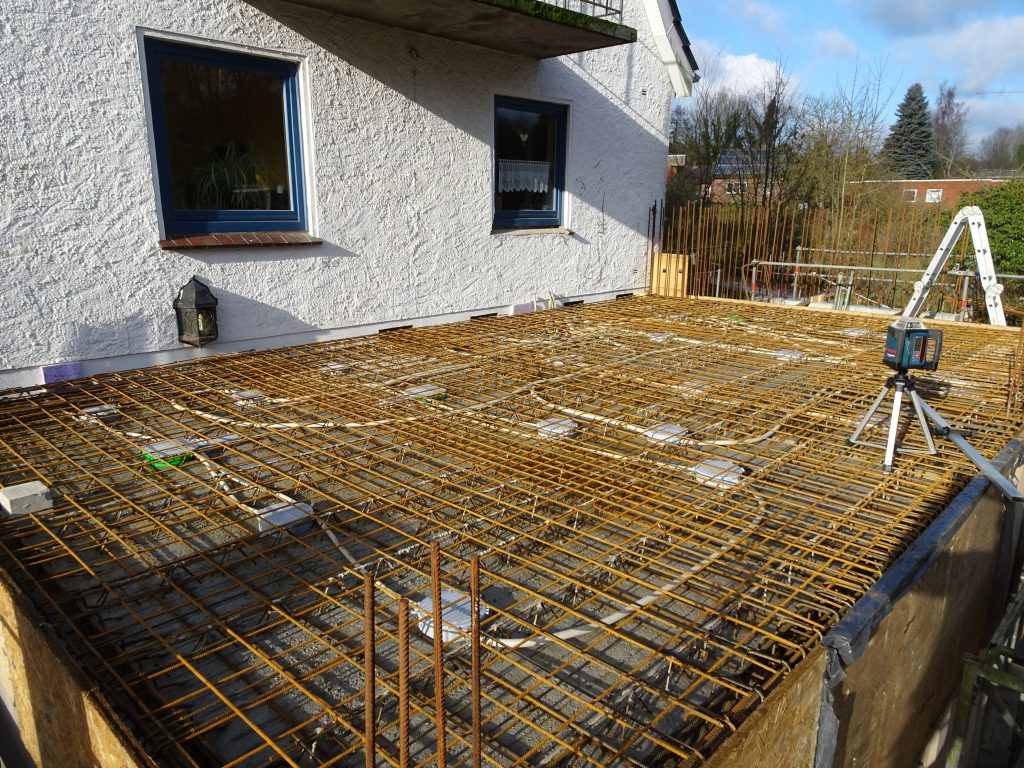
Nach ein paar Stunden waren alle Matten auf der Decke und auch gut positioniert. Endlich konnten wir auch die Anschlußbewehrung für den Ringanker feströdeln.
Über dem Stahl des Isokorbs haben wir die Matte ausgeschnitten, wir hatten den Eindruck dass unser Stahlsandwich etwas zu hoch wird. Auch am Nordrand und direkt an der Hauswand haben wir den Stahl teilweise nicht mit der Matte abgedeckt da dort die dicken Bewehrungsstähle aufgelegt sind.
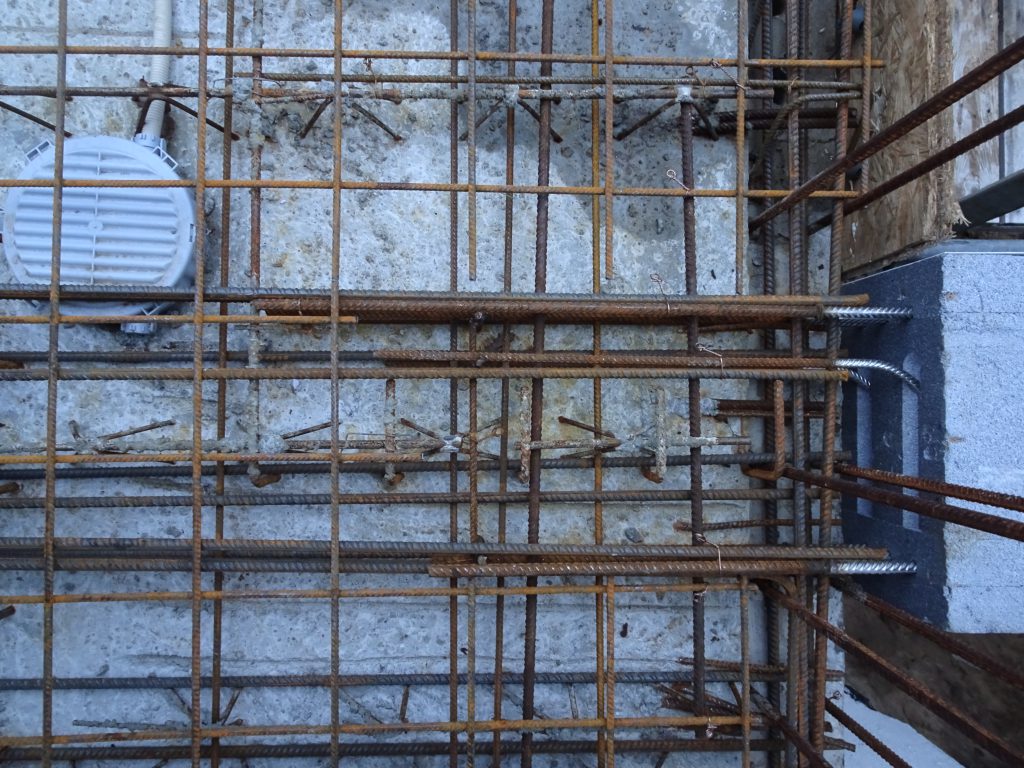
Nachdem wir nochmal alles überprüft und alle beweglichen Teile noch auf den Gitterträgern befestigt hatten, haben wir die theoretische Betondeckung gemessen. Referenz war dabei für uns die bereits vorhandene Schalung.
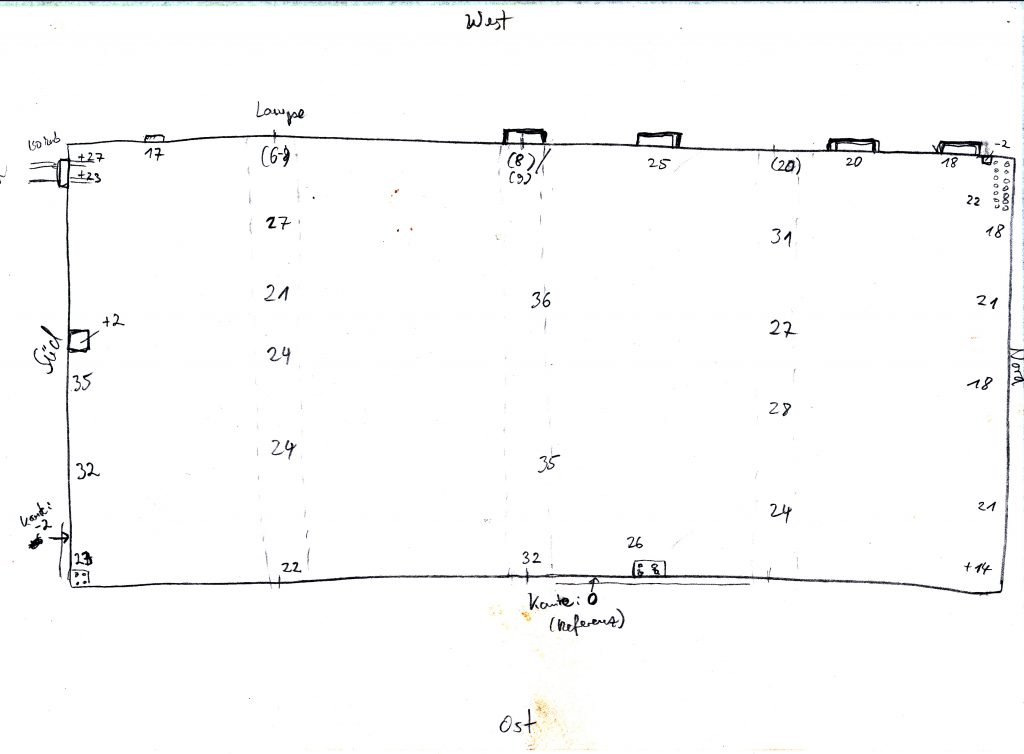
Oben in der Mitte (West) treffen der Stahl für die Auflagertasche, Verstärkung in Nord-Süd-Richtung sowie die überlappenden Matten aufeinander. Dadurch bleiben nur noch 8 mm Betondeckung über. Um eine gewisse Mindestdeckung in diesem Bereich zu erreichen müssen wir mindestens 1 cm mehr Beton vorsehen. Vor dem Umplanen auf Elementdecken war eine Mindestbetondeckung von 25 mm gefordert. Die Pläne, die zusammen mit den Elementdecken erstellt wurden, weisen eine Mindestdeckung von 15 mm aus. Es scheint mehrere Wahrheiten zu geben …
Am Sonntag noch ein wenig Aufregung, der Stahl mit der Nummer 58 ist verschwunden, nur der Zettel taucht wieder auf. Wir stellen Baustelle und Keller auf den Kopf, nicht zu finden. Während des Mittagessens dann die Erleuchtung, Der Stahl wurde zweckentfremdet um den Sturz über der Eingangstür im Souterrain zu erstellen. Der Stahl passte dafür ziemlich gut, war aber eigentlich für die Verstärkung des Isokorbs vorgesehen. Da hat der Bauherr wohl beim Bestellen was übersehen … :-|.
Nach diesem Wochenende hat die Jacke der Bauherrin mindestens ein Loch mehr und unsere Klamotten sind rostrot marmoriert.
Was fehlt noch ?
- Ein Stück Verschalung zwischen Isokorb und Hauswand
- Erhöhen oder Aufdoppeln der Verschalung um 1 cm
- Abdichten von Lücken zwischen Elementdecke und Souterrainwand
- Abdichten der Kabel- und Rohrdurchführungen
- Stahlstütze
- Dübelmarker für das Geländer an der Nordseite